How Digital Twin Software Is Revolutionizing Manufacturing
In the ever-evolving landscape of manufacturing, staying ahead requires more than just automation and efficient workflows—it demands foresight, real-time decision-making, and a comprehensive understanding of every component in the production chain. Enter Digital Twin software—a revolutionary technology that is transforming how manufacturers design, operate, and maintain their operations.
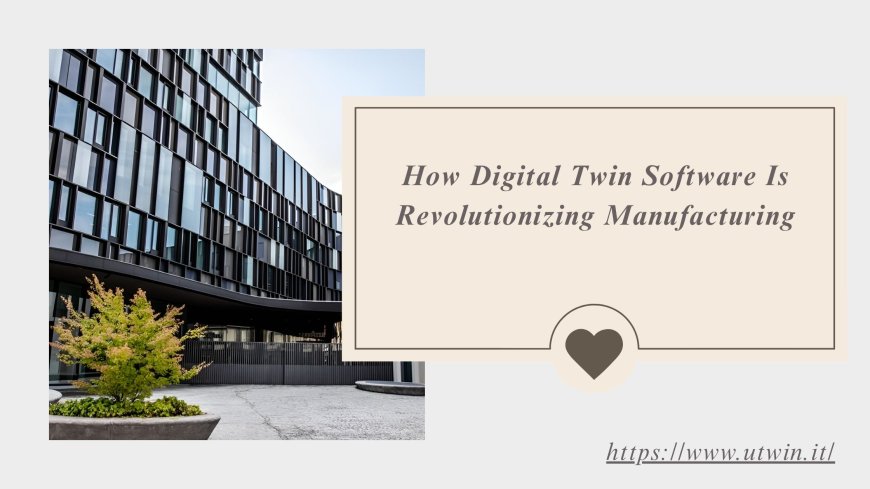
What Is Digital Twin Software?
A digital twin is a virtual replica of a physical asset, system, or process. It mirrors its real-world counterpart in real time using data collected from sensors, Internet of Things (IoT) devices, and integrated software systems. Digital twin software enables businesses to simulate, analyze, and optimize operations without disrupting the actual process.
In manufacturing, this means creating virtual models of machinery, production lines, and even entire factories to monitor performance, predict failures, and improve efficiency.
Bridging the Physical and Digital Worlds
One of the most powerful aspects of digital twin technology is its ability to bridge the physical and digital worlds. By creating an exact digital counterpart, manufacturers gain insights that were previously impossible to obtain. These digital twins allow engineers to simulate various production scenarios, monitor real-time performance, and implement predictive maintenance strategies.
For example, if a machine begins to operate outside of its normal parameters, the digital twin will immediately detect this anomaly. Maintenance teams can then act proactively, preventing costly downtime and reducing wear-and-tear on equipment.
Benefits of Digital Twin Software in Manufacturing
1. Predictive Maintenance and Downtime Reduction
One of the primary advantages of digital twin software is predictive maintenance. Traditional maintenance schedules rely on set intervals, often leading to unnecessary part replacements or unexpected breakdowns. Digital twins, however, use real-time data to predict when a component is likely to fail. This helps minimize unplanned downtime and extends the lifespan of machinery.
2. Improved Product Design and Innovation
Digital twin software allows manufacturers to test new product designs in a virtual environment before creating physical prototypes. This not only saves time and resources but also accelerates the innovation process. By simulating how a product will perform under various conditions, engineers can make data-driven design improvements before the product hits the production floor.
3. Real-Time Performance Monitoring
With digital twins, manufacturers can monitor the performance of equipment and production lines in real time. Operators can track key metrics such as temperature, vibration, energy consumption, and output levels. This visibility enables immediate adjustments to maintain optimal efficiency and quality.
4. Increased Operational Efficiency
By analyzing production processes through digital twins, manufacturers can identify bottlenecks, inefficiencies, and energy waste. These insights lead to smarter decision-making and process improvements that boost productivity, reduce costs, and enhance sustainability efforts.
5. Enhanced Quality Control
Digital twins can be used to simulate and monitor quality assurance processes. Any deviation from standards can be flagged instantly, allowing manufacturers to take corrective actions before defective products are produced or shipped.
Use Cases Across the Manufacturing Spectrum
Automotive Industry
Digital twin technology has become a game-changer in the automotive industry. Car manufacturers use digital twins to monitor the entire vehicle lifecycle—from design and assembly to performance and maintenance. This reduces the need for physical prototypes, shortens time to market, and ensures higher product quality.
Aerospace and Defense
In aerospace, digital twins help simulate aircraft components under extreme conditions, allowing engineers to optimize for safety and durability. Real-time data from sensors on operational aircraft is fed back into digital models for ongoing improvements.
Consumer Goods and Electronics
Companies producing consumer electronics and goods utilize digital twins to simulate production processes, identify design flaws, and ensure high-speed production lines are operating at peak performance.
Overcoming Implementation Challenges
While the advantages of digital twin software are clear, implementation can present challenges. High initial costs, integration with legacy systems, and the need for skilled personnel can be barriers to adoption. However, as technology matures and becomes more accessible, these obstacles are increasingly surmountable.
Manufacturers are encouraged to start with pilot projects—creating digital twins for a single machine or production line—before scaling across their operations. Cloud-based platforms and vendor support also make it easier to implement and manage digital twins without extensive in-house infrastructure.
The Future of Manufacturing with Digital Twins
The digital twin revolution is just getting started. As Artificial Intelligence (AI), Machine Learning (ML), and IoT technologies continue to evolve, the capabilities of digital twins will only expand. Future digital twin systems will become more autonomous, capable of self-diagnosis, self-optimization, and even self-repair.
Moreover, the integration of digital twins with augmented reality (AR) and virtual reality (VR) will allow engineers to interact with virtual models in immersive environments, enhancing collaboration and accelerating innovation.
Conclusion
Digital twin software is reshaping the manufacturing industry by providing a dynamic, data-driven view of operations. From reducing downtime and improving product quality to accelerating innovation and optimizing efficiency, the benefits are undeniable.
As manufacturers continue to embrace digital transformation, those who leverage the power of digital twin technology will gain a significant competitive edge—streamlining processes, reducing costs, and delivering higher-quality products faster than ever before.