How Does a CNC Machine Shop Ensure Accuracy?

How Does a CNC Machine Shop Ensure Accuracy?
In today’s competitive manufacturing landscape, precision and efficiency are not just preferences they are necessities. CNC (Computer Numerical Control) machining has revolutionized the way industries produce complex parts with exceptional precision. However, the real strength of a CNC machine shop lies not only in its advanced technology but in how it ensures accuracy throughout the machining process. From the selection of raw materials to the final quality control inspections, every step plays a role in delivering flawless components.
Understanding CNC Machining
CNC machining is a subtractive manufacturing process where pre-programmed computer software dictates the movement of machinery and tools. The system automates processes such as milling, turning, drilling, and grinding, allowing for high precision, repeatability, and consistency in the production of parts.
Accuracy in CNC machining refers to how close the final product matches the design dimensions specified in the CAD (Computer-Aided Design) model. Maintaining this level of precision is a combination of various technical, mechanical, and procedural elements.
Note:- High-quality parts had been produced at our cnc machine shop, ensuring consistency and durability across every project. Complex tasks had been handled with accuracy and expertise. Your next project deserves the same excellence reach out to Raysun now.
Importance of Accuracy in CNC Machining
Accuracy is critical in industries such as aerospace, automotive, medical devices, and electronics. A minor deviation from the design specifications can result in equipment malfunction, product recalls, or even hazardous failures. Thus, CNC machine shops adopt a variety of strategies to guarantee parts meet strict tolerances and customer expectations.
Machine Calibration and Maintenance
To ensure consistent output, CNC machines must be routinely calibrated and maintained. Calibration involves comparing machine output to known standards and making necessary adjustments.
- Scheduled maintenance: Lubrication, alignment, and part replacement ensure that machines operate at peak efficiency.
- Regular inspection: Axis alignment, tool wear, and sensor functioning are checked to avoid drift from intended measurements.
- Environmental monitoring: Temperature, humidity, and dust control play vital roles in maintaining equipment stability.
Properly maintained machines are less likely to develop mechanical errors that can affect the precision of finished parts.
Skilled Programming and CAD/CAM Integration
One of the foundational elements of CNC accuracy is the precision of programming. The conversion of CAD models into CAM (Computer-Aided Manufacturing) instructions must be flawless.
- G-code accuracy: The G-code that drives machine operations must be optimized and error-free to avoid flawed movements.
- Simulation software: Advanced simulation tools detect potential toolpath errors or collision risks before machining begins.
- Tool selection and pathing: The right tool geometry, speed, and feed rates are chosen for each material and design.
Highly trained CNC programmers are essential in interpreting engineering drawings and converting them into efficient machine code.
High-Quality Tooling and Fixtures
Even with perfect programming, poor-quality tools or unstable work-holding can compromise accuracy.
- Precision tooling: High-end cutting tools with tight manufacturing tolerances help achieve smoother finishes and accurate dimensions.
- Tool wear monitoring: Wear and tear can lead to inaccuracies; shops often use sensors or software to track tool condition in real-time.
- Custom fixtures: Well-designed jigs and fixtures ensure parts remain stationary and correctly oriented during machining.
Rigid setups reduce the chance of part movement or vibration that could distort the final product.
Advanced CNC Machines and Technology
CNC machine shops invest in modern machines equipped with innovative features designed to support precision.
- Multi-axis capabilities: 4-axis and 5-axis machines provide enhanced flexibility and reduce the need for repositioning, which can introduce errors.
- Feedback systems: Encoders and linear scales feed real-time data back to the machine controller, adjusting movements on-the-fly.
- Thermal compensation: Temperature changes can cause material expansion; modern machines use compensation algorithms to adjust accordingly.
These technological advancements significantly reduce the margin for error in complex part production.
Material Selection and Inspection
Accurate machining also depends on the consistency and quality of the raw material.
- Certified materials: Reputable suppliers provide material certification to confirm consistency in composition and properties.
- Pre-machining inspection: Raw materials are often inspected for flatness, hardness, and other critical properties.
- Stress-relieving treatments: Materials are sometimes heat-treated before machining to minimize internal stresses that can affect accuracy.
A uniform starting material reduces variability in the machining process and improves the repeatability of results.
Quality Control and Metrology
One of the most important aspects of ensuring CNC accuracy lies in post-machining inspection. Quality control processes involve checking the final product against the original specifications using high-precision measuring tools.
- Coordinate Measuring Machines (CMM): These devices inspect parts with sub-micron precision, comparing them directly to the CAD model.
- Optical comparators and laser scanners: Non-contact methods provide detailed surface and dimensional analysis.
- In-process inspection: Some machines have built-in probing systems to inspect parts during machining, allowing for real-time corrections.
- Statistical Process Control (SPC): Data from batch production is analyzed to identify trends and deviations before they become critical.
A comprehensive quality control program is essential for minimizing waste and maintaining customer confidence.
Operator Expertise and Training
Even with the most advanced equipment, the human element plays a crucial role in CNC accuracy. Skilled machinists and operators are trained to understand tolerances, machine behavior, and setup procedures.
- Blueprint reading: Operators must accurately interpret technical drawings and understand geometric dimensioning and tolerancing (GD&T).
- Manual adjustments: Operators can make on-the-spot changes or recalibrate setups based on part feedback.
- Continuous education: As technology evolves, ongoing training ensures staff stay updated with the latest techniques and machine features.
Experienced professionals are often the first line of defense against errors during setup and production.
Process Standardization and Documentation
Standard operating procedures (SOPs) and thorough documentation help ensure consistent accuracy across different jobs and shifts.
- Process validation: Each new part goes through a pilot run where the machining process is validated before full-scale production.
- Work instructions: Clearly written instructions guide operators through each stage of production to avoid inconsistencies.
- Change control: Any modifications to the process, tooling, or program are documented and approved through a formal system.
Such controls reduce human error and ensure that all parts are produced to the same high standard.
Use of Automation and Robotics
Automation contributes to accuracy by minimizing human handling, which can introduce variability.
- Automated part loading: Robotic arms or pallet changers can load and unload parts with high precision.
- Automated inspection: Robots can perform measurements and report deviations immediately for corrective actions.
- Unattended machining: Lights-out manufacturing allows parts to be produced overnight under continuous monitoring systems.
By reducing the need for manual labor in repetitive tasks, automation leads to more consistent and precise production.
Feedback Loop and Continuous Improvement
Modern CNC shops employ feedback systems and continuous improvement methodologies such as Lean and Six Sigma to enhance accuracy over time.
- Root cause analysis: Any defect is thoroughly analyzed to determine the underlying cause and prevent recurrence.
- Customer feedback: Input from clients on product quality and fit is used to refine processes and enhance performance.
- Process audits: Periodic reviews of workflows and procedures identify areas where small changes can yield greater precision.
This focus on incremental improvement fosters a culture of accuracy and accountability.
Conclusion
A CNC machine shop does not rely on a single element to ensure accuracy it is a blend of technology, expertise, procedures, and continuous improvement. From the moment a design is created to the final quality check, each stage is meticulously planned and executed. High-end machinery, expert programming, quality tooling, rigorous inspection, and skilled personnel come together to achieve the precise tolerances demanded by modern industries. In an environment where even microns matter, these practices form the backbone of reliable and accurate CNC machining.
For More Isightful Articles Related To This Topic, Feel Free To Visit:- newswireengine
What's Your Reaction?
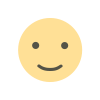
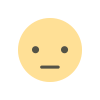
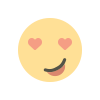
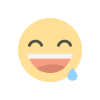
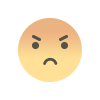
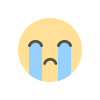
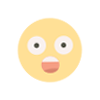