Why Gasless MIG Welders Are Perfect for Windy and Outdoor Welding Conditions ?
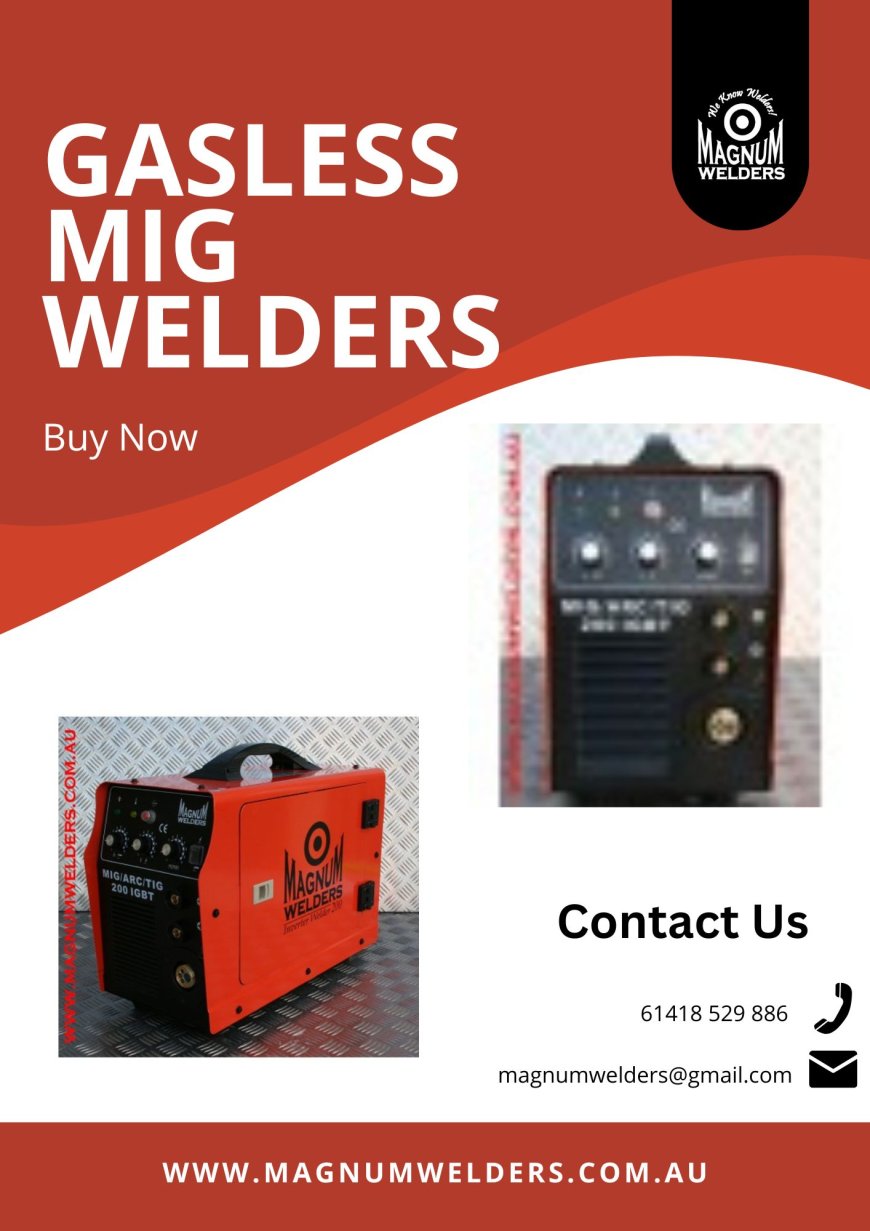
For proper safety and visibility, a number of crucial components should be taken into consideration while selecting a welding helmet. First and foremost, auto-darkening filters are crucial because they, on their own, change the shade of the lens as per the brightness of the arc, shielding your eyes from damaging UV/IR rays while maintaining clear vision while you're not welding. To improve overall job precision and a clear vision, look for helmets with a large viewing area. Shade levels can be changed to suit various welding jobs; they typically range from 9 to 13. Another important thing to focus on as per the reaction time; quicker reaction times offer more protection during unexpected flashes. Long-term strain-free use can be ensured with an adjustable headpiece and a lightweight, comfortable design. Helmets with grind mode are also adaptable, allowing you to switch between welding and grinding without switching gears. Finally, solutions that are battery-assisted or solar-powered offer dependability and convenience. These qualities of Welding Helmets work together to offer the highest comfort, visibility, and eye protection for welding that is both safe and efficient.
Why are gasless MIG welders appropriate for windy, outdoor environments?
Glassless MIG welders, sometimes referred to as flux-cored welders, have become more and more well-liked due to their adaptability and capacity to function well in demanding conditions. In contrast to conventional MIG welders, which depend on an external shielding gas, gasless variants employ a unique flux-cored wire, which makes them particularly appropriate for windy and outdoor environments.
1. No requirement for an external shielding gas:
A separate gas cylinder is not necessary for Gasless MIG Welders. Instead, they use flux-cored wire that creates its own shielding gas as it burns. This eliminates the risk of wind blowing away the protective gas, a common issue with traditional MIG welding outdoors. As a result, the weld remains protected from contaminants, making sure of better quality.
2. Portability and easy to use:
Without the need to carry gas tanks, MIG welders are more portable and easier to set up. This makes them ideal for fieldwork, remote job sites, or quick repair tasks in outdoor locations. Because of their convenience, welders can operate more productively without having to worry about handling extra equipment.
3. Deep penetration on soiled or rusty metal:
Flux-cored wire, which is utilized in MIG welders, offers superior forgivingness and deep penetration on soiled, rusted, or painted surfaces. This reduces the requirement for intensive preparation, which is advantageous for outdoor applications where metal may not always be clean or in optimal condition.
Conclusion:
Because of its self-shielding wire, mobility, and robust performance on imperfect surfaces, gasless MIG welders are very useful in outdoor and windy environments. Because of these qualities, they are a dependable option for welders who require durability and adaptability in erratic circumstances.