How to Use an Image to PES Converter Like a Pro
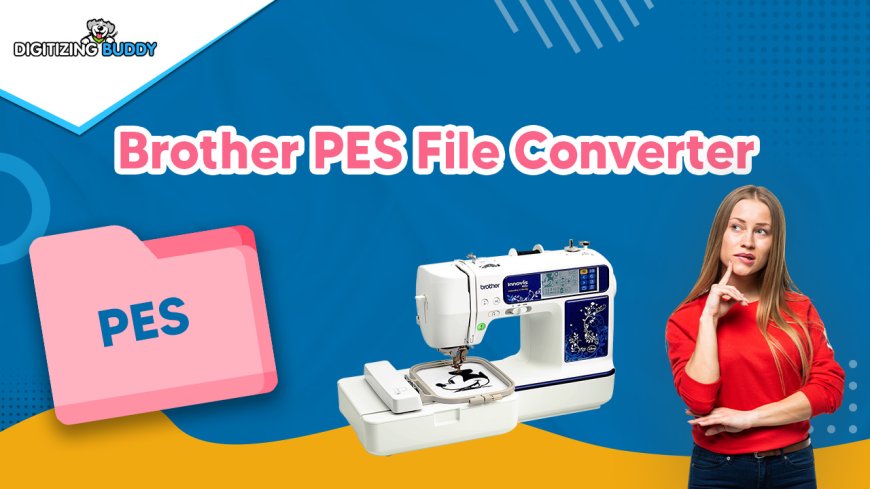
If you’ve ever wanted to turn your favorite image into an embroidered masterpiece, you’ve probably heard about PES files. These files are the magic ingredient that tells your embroidery machine exactly how to stitch your design. But how do you convert a regular image—like a JPEG or PNG—into a PES file? That’s where an image to PES converter comes in.
Whether you’re a hobbyist, small business owner, or just love DIY embroidery, learning how to use these tools properly can save you time, money, and frustration. Let’s break it all down—what PES files are, how converters work, and how to get the best results every time.
What Is a PES File?
Before diving into converters, it helps to understand what a PES file actually is. PES is a file format used by Brother embroidery machines. It contains all the instructions needed for stitching—things like thread colors, stitch types, and the order in which the machine should sew each section.
If you have a different brand of machine (like Janome, Bernina, or Singer), you might need a different format (like .DST, .EXP, or .JEF). But PES is one of the most common, so knowing how to create it is super useful.
Why Convert an Image to PES?
You might be wondering: Can’t I just load any picture into my embroidery machine? Unfortunately, no. Regular images (JPEG, PNG, etc.) are made of pixels, while embroidery machines need stitch data. That’s where conversion comes in.
Here’s why converting an image to PES is essential:
- Machines Need Specific Instructions – A PES file tells the machine where to place each stitch.
- Avoid Pixelation & Blurry Results – Straight-up stitching a JPEG would look messy.
- Control Stitch Types & Density – You can adjust how the design translates into thread.
How Image to PES Converters Work
There are two main ways to convert an image to PES:
- Auto-Digitizing Software – Programs that automatically generate stitch patterns.
- Manual Digitizing Services – Professionals who fine-tune the design for perfect stitching.
Since most hobbyists and small businesses use auto-digitizing tools, we’ll focus on those.
Step 1: Choose the Right Converter
Not all converters are equal. Some free tools produce low-quality files, while paid software gives better control. Here are a few popular options:
- Wilcom TrueSizer (Free for basic conversions)
- SewArt (Auto-digitizing software)
- Ink/Stitch (Free, open-source option for advanced users)
- Online Converters (Quick but often lower quality)
For best results, avoid super basic online converters—they often create messy, inefficient stitch patterns.
Step 2: Prepare Your Image
Before converting, optimize your image for the best results:
- Use High-Contrast Images – Simple, bold designs work best.
- Remove Backgrounds – If your image has a busy background, erase it first.
- Simplify Complex Details – Tiny text or fine lines may not stitch well.
Step 3: Upload & Adjust Settings
Once you’ve picked your software, upload your image and tweak these settings:
- Stitch Type (Satin for text, Fill for large areas)
- Stitch Density (Too dense = stiff fabric; too light = gaps)
- Underlay Stitches (Helps prevent fabric puckering)
- Thread Colors (Match to your available threads)
Step 4: Test Before Stitching
Never skip this step! Stitch out a sample on scrap fabric to check:
- Are the details clear?
- Does the fabric pucker?
- Are there any thread breaks or misalignments?
If something’s off, go back and adjust the digitizing settings.
Common Problems (And How to Fix Them)
Even with a good converter, you might run into issues. Here’s how to troubleshoot:
1. Jagged or Pixelated Stitches
- Cause: The original image was low-resolution.
- Fix: Use a vector file (SVG, AI) or a high-quality PNG.
2. Thread Breaks or Tension Issues
- Cause: Stitch density is too high.
- Fix: Reduce stitch density or adjust tension settings.
3. Fabric Puckering
- Cause: Not enough underlay stitches.
- Fix: Add a zigzag or mesh underlay for stability.
4. Colors Not Matching
- Cause: The software’s thread palette doesn’t match your threads.
- Fix: Manually adjust thread colors in the PES file.
When to Use Professional Digitizing Instead
Auto-digitizing is great for simple designs, but complex logos or detailed artwork often need a human touch. Here’s when to consider hiring a pro:
- Small Text & Fine Details – Machines struggle with tiny elements.
- Gradients & Shadows – Converting these smoothly requires manual tweaking.
- Large Designs – Professionals optimize stitch order to prevent fabric distortion.
If you’re selling embroidered products, investing in professional digitizing can save you from costly mistakes.
Final Tips for Perfect PES Files
Want pro-level results without the pro price tag? Follow these best practices:
✔ Start Simple – Basic shapes and bold fonts convert best.
✔ Use Vector Files When Possible – They scale perfectly without losing quality.
✔ Test on Similar Fabric – Different materials behave differently under stitches.
✔ Keep Backup Files – Save your PES file in multiple formats in case you switch machines.
Wrapping Up
Converting an image to PES doesn’t have to be intimidating. With the right tools and a bit of practice, you can turn any design into a stunning embroidered piece. Just remember:
- Good prep = better results (clean, high-contrast images work best).
- Test before final stitching (saves time and materials).
- Know when to go pro (some designs need manual digitizing).
Now that you know the ins and outs of image-to-PES conversion, why not give it a try? Pick a design, fire up your converter, and start stitching like a pro!